Profiles
|
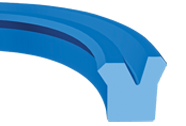 | Rod Single Lip Unloaded U-Cup
The rod style unloaded U-cup was designed with a shorter, heavier inside sealing lip to achieve a higher initial sealing force on the tube. The rod style unloaded U-cup was developed to extend serviceability and improve reliability in rod sealing.
|
|
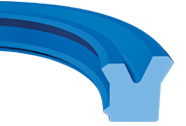 | Rod Double Lip Unloaded U-Cup
The rod style unloaded U-cup is available in a double lip design. The secondary �bump� or lip on the inside heel of the seal provides additional stability in the seal groove. The increased stability enhances the long-term performance of the seal. In rod seal leakage test, the double-lipped rod style unloaded U-cup had better performance then the conventional U-cup. This is due to the initial leakage of the seal is being reduced by the secondary sealing lip.
|
|
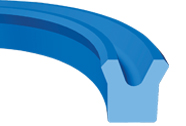 | Symmetrical Unloaded U-Cup
This design provides satisfactory service for most rod and piston sealing applications. For more demanding applications with higher temperatures and pressure, other designs should be considered. |
|
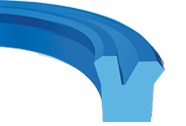 | Piston Unloaded U-Cup
The piston style unloaded U-cup was designed with a shorter, heavier outside sealing lip to achieve a higher initial sealing force on the tube. The piston style unloaded U-cup was developed to extend serviceability and improve reliability in piston sealing.
|
|
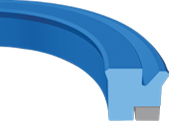 | Piston Unloaded U-Cup with Anti-Extrusion Ring
Unloaded piston U-cups are also available with anti-extrusion rings. The profile fits a standard u-cup gland, while providing increased extrusion resistance.
|
Design Considerations:
Surface Finish
The chart below provides a general guideline on surface finish.
|
Static |
8-32 RMS | Dynamic |
16 RMS | |
Pressure/Velocity
Pressure and velocity are two of the factors that will affect seal integrity. The unloaded urethane U-cup is designed to operate between 0 to 250 feet per minute at 1000-3500 psi. However, the unloaded U-cup can operate at up to 900 feet per minute in low or negligible system pressures. The unloaded urethane U-cup�s performance varies depending on temperature, lubrication, and the chemical environment. Performance capabilities can be extended with the use of an anti-extrusion ring. |
|