KasPex™ PEEK is Quality and Quality is Strength! |
KasPex™ PEEK is Hi-Tech Seals’ family of high-performance thermoplastic PEEK. These compounds provide durability in harsh chemical environ-ments, excellent mechanical strength, and remarkable dimensional stability. KasPex™ PEEK offers hydrolysis resistance in hot water and steam. This family of PEEK improves the performance and reliability of machined parts in innumerable applications, with new end uses being discovered on a regular basis.
KasPex™ PEEK advantages:
- Outstanding chemical resistance
- Superior high temperature performance
- Exceptional wear & abrasion resistance
- High electrical integrity
- Excellent hydrolysis resistance
|
|
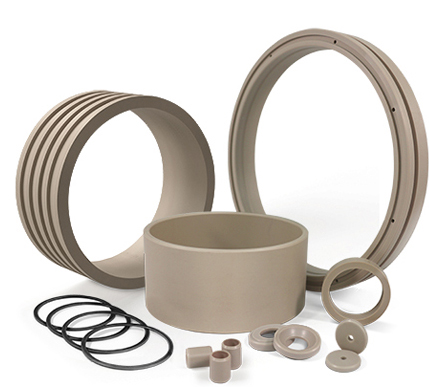 |
The KasPex™ PEEK family of materials
is composed of various compounds
including:
- MP39 is our virgin PEEK that offers the highest elongation,
toughness, and inertness of all the KasPex™ materials
- MP38 high temperature performance MP38 is our glass reinforced PEEK which provides additional rigidity and stability
- MP37 is our carbon reinforced PEEK which provides lower coefficient of friction
|
Physical Properties |
ASTM |
MP39* |
MP38* |
MP37* |
Hardness, Shore A |
D2240 |
87 |
87.5 |
90 |
Tensile Strength, psi (MPa) |
ISO 527 |
100 |
171 |
234 |
Elongation, % |
ISO 527 |
54 |
2.6 |
1.8 |
Specific Gravity |
ISO 1183 |
1.30 |
1.51 |
1.40 |
*Typical values for injection moulded specimen.
|
KasPex™ PEEK has a general temperature range of -70°C to 260°C (-94°F to 500°F), specialty compounds are available for low
temperature and extreme heat applications. It is used in numerous critical applications across an endless number of markets and
industries, including: |
- Oil & gas
- Semiconductors
- Medical & pharmaceutical
- Chemical
|
- Automotive
- Agriculture
- Conveyor technology
- Plant processing
|
For more information on KasPex™ PEEK materials, email our engineering department at engineering@hitechseals.com. |
*The above information is correct based on our knowledge at the date of its publication. The temperature range listed is a general guideline and final suitability will depend on various application conditions. To ensure this material meets customers’ final requirements and safety demands, we recommend customers conduct their own testing. |
|
|